5 Effective Methods for Identifying Blind Spots in Your Supply Chain
Boost efficiency and minimise risks.
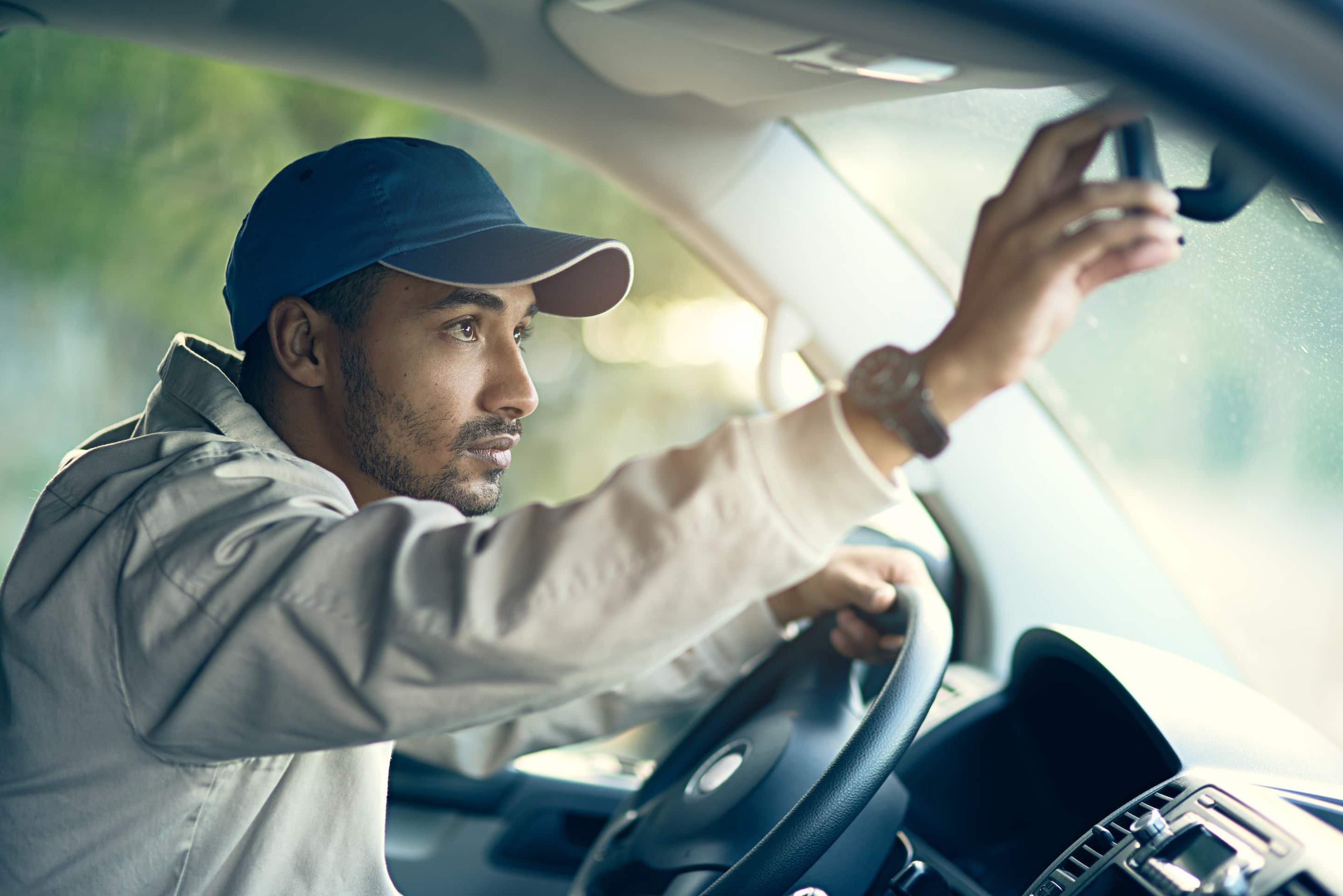
When you think about the many various factors that all contribute to successful, seamless supply chain management—from having access to a reliable carrier network, to accurate inventory and warehouse management—visibility is the one key element that ties everything together. Without detailed visibility over the supply chain, shippers are navigating in the dark. A lack of visibility means that a supply chain manager is unable to predict, respond or adapt to the complexities of the freight industry.
Is visibility the most important factor in the supply chain?
For shippers, visibility is the linchpin that holds a resilient and responsive supply chain together. Accurate and detailed visibility enables shippers to mitigate risks, enhance efficiency, and meet customer expectations. Overall, it leads to improved decision-making, where shippers have the information and data they need to make informed choices. Sometimes, these decisions need to be made as quickly as possible. Improved visibility allows shippers to make the right call, even when placed under strict time constraints.
The beneficial knock-on effects of enhanced visibility
Beyond the immediate benefits of enhanced visibility, other knock-on effects can influence every facet of the supply chain logistics process:
- Streamlined inventory management: Accurate tracking reduces inventory discrepancies, leading to more efficient stock management.
- Sustainable practices: Optimised routing and reduced idle times contribute to lower carbon emissions, aligning with sustainability goals.
- Stronger supplier relationships: Transparency fosters trust and collaboration between shippers and their suppliers, as well as the carriers, enhancing the supply chain's resilience against disruptions.
- Market responsiveness: With better visibility, shippers can quickly adapt to market demands and trends.
How better visibility can give you a competitive advantage
In the competitive logistics industry, better visibility within your supply chain is an operational advantage and a valuable strategic asset.
Proactive problem solving
Think of it this way: visibility is the one thing that can take your business from “reactive” to “proactive”. With real-time insights into the supply chain, shippers can identify and address issues before they escalate, preventing costly delays and maintaining service reliability. This proactive approach not only saves resources but also safeguards your reputation as a shipper.
Optimised operations
Enhanced visibility allows for the fine-tuning of logistics operations, from managing inventory to delivery schedules. This gives shippers the ability to reduce excess inventory, minimise storage costs and optimise route planning, leading to cost savings and operational efficiency.
Customer loyalty
Customers value transparency. Being able to meet customer demands and provide clients with accurate updates on their shipments can help foster trust and brand loyalty, differentiating you from other shippers in the market.
Data-driven decisions
Access to comprehensive data enables shippers to analyse trends, predict future challenges, and make informed strategic decisions. This insight can reveal opportunities for innovation, allowing shippers to remain agile, adapt their services and meet changing customer needs.
Common shipping blind spots
No one said that navigating the complexities of the logistics industry was easy. Shippers often encounter unforeseen problems in the shape of unexpected weather, global events, and world economic shifts. However, one step towards overcoming these large (and sometimes unavoidable) obstacles is to recognise common shipping blindspots that could be hampering your ability to remain agile, flexible and proactive, and therefore your capacity to ensure goods are delivered on time.
Supply chain blind spots you might have missed
Several blind spots can disrupt the smooth operation of supply chains, often overlooked until they cause significant issues:
- Inaccurate inventory data: Misalignment between physical stock and inventory records can lead to stockouts or excess inventory, affecting order fulfilment and customer satisfaction.
- Lack of real-time updates: Without real-time visibility into the whereabouts of shipments, shippers cannot accurately predict delivery times or address delays proactively.
- Poor communication: Ineffective communication between shippers, suppliers and carriers can result in misinformation and delays, impacting the entire supply chain's efficiency.
- Inflexible supply chains: A lack of adaptability to changes in demand or supply chain disruptions can lead to significant inefficiencies and increased costs.
- Weak data security: Vulnerabilities in data management and sharing can lead to breaches, affecting operations and trust.
Addressing these blind spots requires a strategic approach, leveraging technology to enhance visibility and streamline processes.
How to recognise visibility gaps in your supply chain
Recognising visibility gaps is crucial for shippers aiming to improve logistics operations and drive efficiency. Identifying these blind spots is the first step towards implementing solutions that ensure a smooth and transparent supply chain process, which is crucial for maintaining your competitive edge in the logistics business.
5 Steps to identify blind spots in your supply chain
- Conduct a comprehensive supply chain audit: Begin by mapping out your entire supply chain, including all business logistics operations and inventory management processes. This thorough examination helps highlight areas where data is missing, or processes are not transparent, indicating potential blind spots in your supply chain.
- Leverage technology for data analysis: Utilise analytics tools to examine your supply chain data. These technologies can uncover inconsistencies and inefficiencies in real-time tracking, inventory levels, and order processing times, offering insights into where visibility can be improved.
- Engage with your logistics partners: Communication with your logistics partners, including carriers and logistics managers, is key. Having open conversations with people directly involved in your supply chain is one of the easiest and most effective ways to understand where your potential blind spots may be. Their feedback can provide valuable insights into where breakdowns in communication and visibility occur, helping to pinpoint areas for improvement.
- Monitor key performance indicators (KPIs): Identify and monitor KPIs relevant to your supply chain, such as order accuracy, shipment times, and inventory turnover rates. If you notice that some KPIs are much lower than others, this could signal visibility issues that need addressing.
- Implement a continuous improvement plan: Recognising visibility gaps is an ongoing process, meaning you’ll need to establish a plan for regular reviews and continuous improvement of your supply chain processes. Incorporate feedback mechanisms and stay updated with the latest logistics management technology to adapt and refine your approach.
By following these steps, shippers can effectively identify and address visibility gaps within their supply chains. Solutions like Ofload's end-to-end road freight solution offer the technology and support needed to enhance visibility, streamline operations, and maintain a competitive edge.
Technological solutions to combat supply chain blind spots
Overcoming the visibility challenges in the supply chain for logistics companies demands innovative technological solutions. Ofload’s freight solution offers shippers a centralised, digital supply chain that can help support you across different aspects of your business. By integrating accurate key milestone events, GPS tracking and in-depth data insights, you can gain increased visibility across the supply chain process. This allows you to make more informed decisions, stay updated on your shipments’ status, and ultimately keep your customers happy. Contact Ofload today and discover how our end-to-end freight solution can help support your business.